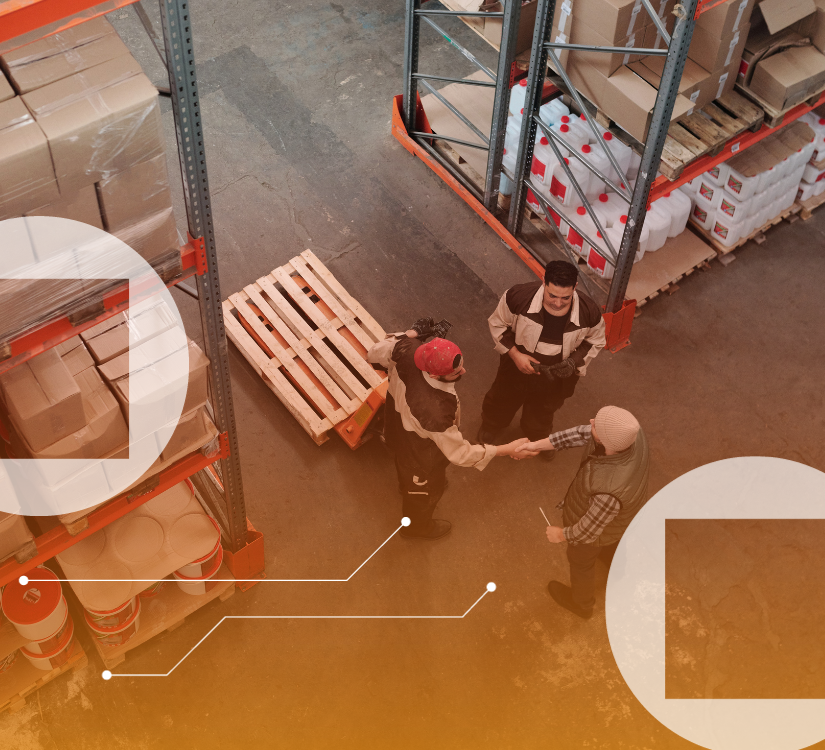
Many manufacturing companies in the past few years have attempted different methods and strategies for staying ahead in the industry. Many have struggled trying to stay ahead of labor shortages combined with global uncertainty, fragile supply chains, and rising costs impact operations across the globe.
Some companies have found success in controlling certain variables within their operation and using LEAN strategies to manage their operation including the 5s method.
But what is this method of operating and how can it help your business?
What is the 5S method?
The 5S method originated in Japan and has been coined as a recent popular trend by Toyota. Due to its multiple benefits, it is quickly gaining momentum for other companies to adopt
It is based on an implementation strategy of each principle starting with the letter ‘S’—Sort (Seiri), Systematize (Seiton), Shine (Seisco), Standardize (Seiketsu), Sustain (Shitsuke). These principles are based on a philosophy of “a place for everything and everything in its place,” which creates a sustainable, effective, and efficient workplace.
How important is it for manufacturing?
All companies at their core need a solid foundation of sustainability and systemization. This may seem hard to achieve, but the 5S method creates essential benefits including:
- Reduction of waste
- Improved efficiency
- Enhanced safety
- Quality improvement
- Employee engagement and morale
By implementing the five principles, manufacturing companies can achieve an economical, and highly effective lean manufacturing operation. And help to create a work environment that is safe and supports improvement and productivity.
Understanding this method and how it can be used for your manufacturing business is important. But it’s necessary to recognize each step’s purpose, and ensure each step is factored into your operation.
The Principles of 5s
- Sort. Identifying and removing unnecessary items from the workplace. This creates a clear distinction between essential and non-essential items.
- Straighten. Organize and arrange items in a manner that promotes a systematic and logical manner. This increases visual management techniques and easy access and retrieval.
- Shine. Implement a cleaning routine and thoroughly sanitize the workplace. This encourages employees to take responisbility for maintaining cleanliness.
- Standardize. Develop and implement work procedures and guidelines. This ensures consistency in standardized processes and provides necessary resources.
- Sustain. Continuing a culture of the 5S practices. Encouraging your employees to follow the practices on a daily basis provides better support and improvement.
It’s important for companies to recognize this method does not simply get applied and fixes everything. It is an ongoing continuous process that takes time and effort to implement successfully. Continuous efforts are required to establish not only an organized and efficient workplace, but instill a culture of quality, productivity, and improvement. By implementing a 5s system, you can help your operation reach greater heights.
Learn about more Lean methods and what benefits they can bring to your operation.